Lean Production is experiencing yet another one of its youth. It has been happening since the 1940s and continues every time the world goes into crisis.
The current crisis is tremendously difficult, even for Lean: there is no time for the big picture, there is an urgent need for companies to have money left over to give energy to the machine, in a context of a great contraction in consumption.
The beginning of Lean Thinking was born in Japan, at Toyota, and was extremely romantic: post-war, very scarce resources, and from there emerged the need to identify a challenging but sustainable reorganizational philosophy. The pivotal principle was the people, their ability to find efficient solutions together and to overcome, step by step, the difficulties, aiming at continuous improvement.
The people were able to look with confidence at their own section of the race, knowing that the interconnection would be done in the best possible way with other colleagues. In short, a fantastic relay race, which managed to lead Toyota and other fantastic change makers to contribute to the development of our planet.
What was the main goal of these people? Improve the 7 MUDAs (waste) as much as possible:
- Defects
- Overproduction
- Transports
- Movements
- Waiting time
- Excessive Stocks
- Complicated Processes
Even today, people are still the only ingredients that make the DIFFERENCE, too bad that in times of crisis people are always forgotten, at least at first.
This is how the eighth muda is generated: DISENGAGEMENT, in other words the waste of solely focusing on performance, forgetting the importance of people engagement.
How long will it be before realizing that the answer to Fordism is not an automated, lights-out factory, but flexibility based on a little less automation and a little more human intelligence? Ah… How much damage has been created so far?!
What I hope is that Modern Lean engineers do not forget the romanticism that marked the development of the great “lean” companies. Engineers, it’s up to you to do yet another restructuring of our planet, even if, today more than ever, a great attention to listening and gratitude for everyone’s contribution is essential.
So let’s take a look at what 2 areas of work can be for “modern” Lean.
1. Work on the characteristics of a Great Team Leader:
- Gratitude and Acknowledgement
- Authenticity and Adaptability
- Innovation, Responsiveness and Simplicity
- Listening, Storyteller and Passionate Team Player
(Surely you will struggle to maintain the holistic approach that Lean assumes)
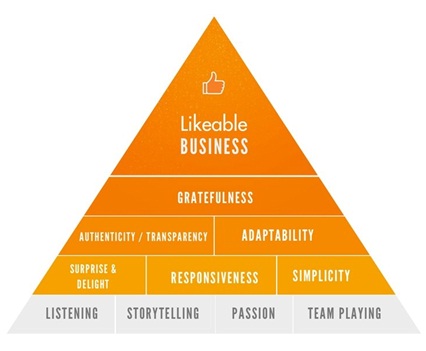
KERPEN, D. (2012). Likeable Business: Why Today’s Consumers Demand More and How Leaders Can Deliver. Macgraw-Hill
2. Work on the characteristics of a great Team and overcome its dysfunctions:
- Trust
- Acting on Feedback
- Unambiguous commitment
- Taking charge
- Always look towards a common goal
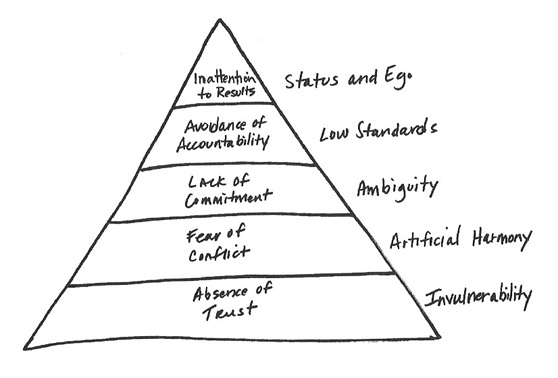
LENCIONI,P. (2007). La guerra nel team. Racconto sulle 5 disfunzioni del lavoro di squadra. ETAS.
Therefore, Lean is also in the loop: “Engaged people make Lean effective, but also, effective Lean makes people engaged.”