La Lean Production sta vivendo una sua ennesima giovinezza. Accade dagli anni ‘40 e continua ogni qualvolta il mondo entra in crisi.
L’attuale crisi è tremendamente difficile, anche per la Lean: non c’è tempo per la big picture, c’è urgente bisogno per le aziende che in cassa restino quattrini per dare energia alla macchina, in un contesto di grande contrazione dei consumi.
L’esordio del Pensiero Lean nasce in Giappone, alla Toyota, ed è estremamente romantico: dopoguerra, risorse scarsissime, da lì emerge la necessità di individuare una filosofia riorganizzativa sfidante ma sostenibile. Il principio cardine erano gli uomini, la loro capacità di trovare soluzioni efficienti assieme e di superare, step by step, le difficoltà, puntando a miglioramenti continui.
Gli uomini riuscivano a guardare con fiducia al proprio tratto di gara, sapendo che l’interconnessione sarebbe avvenuta al meglio con gli altri colleghi. Una fantastica staffetta insomma, che è riuscita a condurre Toyota e altri fantastici change makers a contribuire allo sviluppo del nostro pianeta.
Qual era l’obiettivo principale di queste persone? Migliorare il più possibile i 7 MUDA (sprechi):
- Difetti
- Sovrapproduzione
- Trasporti
- Movimenti
- Attese
- Troppe Scorte
- Processi Complicati
Anche oggi, sono ancora gli uomini i soli ingredienti a fare la DIFFERENZA, peccato che in tempo di crisi delle persone ci si dimentichi, almeno all’inizio, sempre.
Così si genera l’ottavo muda: IL DISINGAGGIO, in altre parole lo spreco di concentrarsi unicamente sulla performance, dimenticando l’importanza dell’engagement delle persone.
Quanto tempo passerà ancora prima di rendersi conto che la risposta al Fordismo non è una fabbrica automatica e a luci spente, bensì la flessibilità basata su qualche automazione in meno e su un po’ d’intelligenza umana in più? Ah…Quanti danni sono stati finora creati?!
Ciò che spero, è che gli ingegneri della Moderna Lean non dimentichino il romanticismo che ha contraddistinto lo sviluppo delle grandi imprese “snelle”. Ingegneri, tocca a voi l’ennesima ristrutturazione del nostro pianeta, anche se, oggi più che mai, è essenziale una grande attenzione all’ascolto e alla gratitudine per il contributo di tutti.
Vediamo dunque quali possono essere 2 aree di lavoro per la “moderna” Lean.
1. Lavorare sulle caratteristiche di un Grande Team Leader:
- Gratitudine e Riconoscenza
- Autenticità e Adattabilità
- Innovazione, Reattività e Semplicità
- In ascolto, Storyteller e appassionante Team Player
(Sicuramente si farà molta fatica a mantenere l’approccio olistico che la Lean presuppone.)
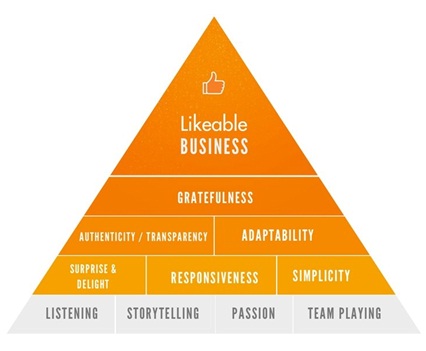
KERPEN, D. (2012). Likeable Business: Why Today’s Consumers Demand More and How Leaders Can Deliver. Macgraw-Hill
2. Lavorare sulle caratteristiche di un grande Team e superarne le disfunzioni:
- Fiducia
- Feedback agito
- Impegno senza ambiguità
- Prendersi in carico
- Guardare sempre a un obiettivo comune
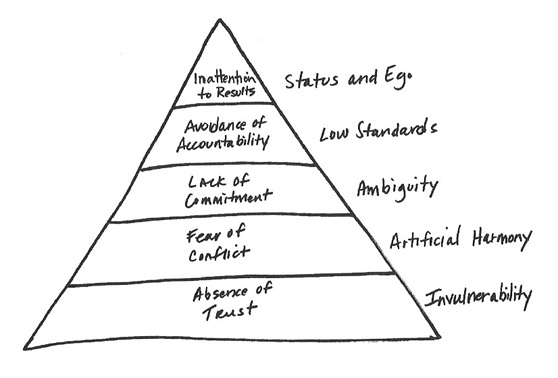
LENCIONI,P. (2007). La guerra nel team. Racconto sulle 5 disfunzioni del lavoro di squadra. ETAS.
Anche la Lean è dunque nel loop: “Le persone ingaggiate fanno la Lean efficace, ma anche, la Lean efficace fa le persone ingaggiate”.